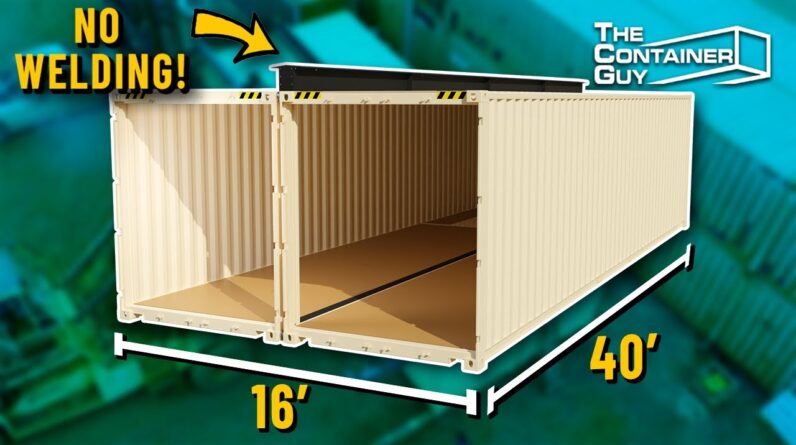
have you ever had the idea of buying two 40-foot shipping containers cutting out the center walls and slapping them together it's a little more difficult than that but in this video we're gonna walk you through the steps and show you an engineered solution to give you a double-wide 40-foot shipping container stay tuned hi i'm channing mccorston the container guy we've received a customer order for a structurally engineered stamped and permitted 40-foot double-wide shipping container we'll be using two 40-foot high cube one-time use containers cutting out the center walls installing structural headers performing a few other modifications shipping them off to the customer in northern alberta and then reassembling on-site what happens often here at the container guy is customers come to us with their problem we work closely with the customer in developing a solution and that is exactly what's happened here this customer we've actually already built them the first prototype double wide shipping container they liked it so much they came back for a second so we've made revision to the design once this kit is finalized all revisions made this will be available to the public for purchase check us out tcg.ca we'll keep you updated on when this is available we're very fortunate that the customer already has a concrete slab on site for their foundation uh if you're gonna cut out the full 40 feet of a container the floor is going to sag so in order to mitigate this floor sag even when on a concrete pad it's still going to sag a half inch or 12 mil because the bottom channel is higher up than the corner castings and so yeah if you just sat a can on concrete it would only touch in the four corners so to mitigate the floor sag even a half inch it's still kind of annoying when you're operating in there we've got a half inch thick flat bar that's four inches wide we'll be installing it underneath the channel stitch welding it all the way across and flush with the corner castings so here we have the first 20 foot length of flat bar clamped on and tacked in place just want to show you the difference between installed and not so that gives us that extra half inch of clearance on the underside of the channel we went over it with the grinder to get all the undercoating off and nice and level so it's not pushing down on the flat bar in weird places so now that we have the flat bar all welded up on the bottom side of the channel there we're gonna get into installing the temporary posts so what we'll do is we'll cut out there's just a small panel section on these 40s from weld to weld we'll cut that chunk out we're gonna weld in our temporary structural post prior to us installing the header and dropping the full 40 feet so that's just going to make sure the header is strong enough to support the weight of the floor and the roof so that temporary post is going to keep the floor from sagging as we handle this thing and as we deliver to the customer until it is set up in place on site so just pop in the shop here and check in on the progress our ticketed red seal journeyman welders have the trusses all tacked together once they're all packed together they'll be clamping them down making sure there's no warpage and then finish welding up all of the seams and edges these trusses are sectioned into 10 to 12 foot lengths this makes them much more manageable once they're all finished up to install on the container so these will all be fully welded white metal sound blasted and then powder coated and then when we go to install these into the container just one at a time they'll be lifted up and bolted into place there'll be no welding after that process performed that's when we start cutting the wall out we finished welding up the header sections and have laid them out all on the floor just to test fit everything we bolted everything together just to make sure proper fitment and no funny gaps so these are now ready to dismantle they'll all fit nicely on one pallet and then they'll ship off to powder coatings so they're going to get a white metal sandblast and then we're going to do our nice textured black finish so we're back in the can the temporary post is now put in uh the next step we're gonna do is uh we're gonna start strut lining the wall we'll do this as we wait for the headers to come back from powder coating so we've uh marked out all of the corrugations every second corrugation we're gonna be installing our csm brackets and then strut lining the wall and eventually be going across the ceiling as well we're doing this in the non-insulated position and what might be kind of funky with this one is that we're actually going to be spray foaming the ceilings so even though they're going to be installed in the non-insulated position and then we're spray foaming we're doing that to handle the snow loads in the arctic so the strut will be very tight to the ceiling and then the spray foam is just going to bridge that final gap and what that's going to do is because snow typically falls off both sides of a container and now we have that long header on the one side where the two containers join the snow can't uh the water can't melt and drip off that side so there's potentially going to be an additional accumulation of snow in here and that could eventually concave the ceiling and who knows collapse it or something so we want to be uh we want to ensure that that whole ceiling is a nice two inch thick slab of foam with some steel structure in there that's going to handle all the weight in the arctic and allow the snow to melt and go off this side for this can and then the other side on the other so on this side of the can this is the wall section that's gonna get removed we're still waiting for the headers to show up from powder coating and we'd like to get at strut lining this and potentially even spray foaming the ceiling prior to installing the uh the header and dropping all the wall panels so this bracket allows us to install strut on the square tube of the container and then it is actually completely out of the way so when the welders are cutting the panel they're not gonna drop my strut on the inside of the can while they're doing it this is getting spray foam so you see it's nice and tight to the ceiling we're going to be doing two inches of spray foam insulation in this one that's going to lock that right in and then this roof corrugation here that's really echoey you know it dimples when you step on it that keeps that nice and stiff now once you got this thing spray foam you jump back on the roof you cannot move that corrugation it's rock solid it's super important to walk through the container with your spray foam contractor the actual sprayer and go through with them what you actually want sprayed and let them know what you don't want overspray on the better the prep work they do ahead of time the better the finish is at the end and the spray foam the the particles that kind of settle in the air and land on things it's it's pretty icky stuff and if it lands on the floor of the container can often discolor it even after you scrape it off so yeah make sure that you poly down on the floor if you're not finishing afterwards and cover off any walls that you're not foaming that you don't want foam stuck to what we're going to have to do is just make sure that we tape off very nicely over top of all of the the csm brackets that we're not over spraying on them and then on the other side we're going to be cutting the wall out we want to make sure that we don't foam the underside of the tubing we just go up to this uh this plane of the the tubing there these guys here at comfort they do a great job taping everything off making sure that we don't over spray anything that shouldn't be sprayed i want to point out the type of tape that they use because it's pretty it's pretty good stuff they i think it's probably it's pretty low cost it's a 3m scotch tape a packing tape brown tape here and so this going over all of the the front face of the unistrut stops phone from getting in there and then it's super simple to rip this stuff off afterwards and doesn't leave any funky residue on the steel surface so for this double wide kit the spray foamers are just doing two inches of insulation on the ceiling but if this was for a container home project our spray foam contractor recommends three inches of spray foam on the walls and the ceiling and typically either the underside or you're going to have to do some sort of rigid foam underneath a subfloor to make sure that you have a nice foam envelope inside of your shipping container so the headers have arrived from powder it's time to jump up there and install them in the can what makes this kit so great is that they're in 10 to 12 foot lengths and so they're relatively easy to handle and get up onto this can all we have to do is just pre-drill and self-threading bolt each header section in if you've watched any of our other videos uh you might start recognizing travis by now he's uh he's our electrician which is kind of interesting to note here because typically when you're doing a header that's going to span an entire 40-foot cut out of a container you need a welder there not an electrician but because these kits are modular and drill and bolt together you know he's a better man for the job than them and furthermore we're just so busy with mods right now that i need his help and he's a good guy to be here and help me and i'm willing to so i appreciate that but yeah travis a r electric you want to size your drill bit for the smaller portion of this thread cutting bolt and then that little notch in the threads that's actually a drill bit so to speak so that will make the hole a bit larger to the size that it needs and it will also start cutting the threads so that you don't need to actually drill right through the 60 millimeter tubing you can just use this bolt they're a case hardened bolt they'll go into the outside of the top tubing but not right through your container and and uh be a thermal bridge so far this just been going together like butter we've been loving it compared to the last time just so refined the the design of it in the 3d model everything's lining up perfectly we haven't had any problems yet and hopefully it continues that way so we've got the first two uh header sections in and we're working our way back we're so confident that we're kind of bolting it up a bit more thinking that we're not going to have to take it down and make any adjustments and we'll see if that decision pans out if you notice a tiny ridge from one truss to the other it's not a problem because the ridge cap that goes after this once the two containers are brought together it's just a ridge basically a peak ridge so there'll actually be a bit of a gap here anyway the ridge cap secures to this outer flange so don't worry if there's a bit of a heap on one side or the other here our electrician has finished bolting up the headers onto the two containers so the next step here now is to have the welders come in and drop the corrugation panels what's super important to note is that we left the panel attached to the container in four different places the one tour over there we got two other places in the middle and then one over there at the end so that just makes sure that when this panel drops it doesn't come back in and take out your ladder just the safety for the uh for the welder that's dropping the panel and then a second thing to note we uh drug a pallet underneath this panel so now once we just finish these few little tacks and drop it down we can come at this with our forklift and lift up this 18 foot sheet and not have it all bendy on us we'll probably use the same pallet and drop all four panels on the same one so we can get this up and out of here and either reuse these panels for other projects or send them off for recycling now that the container is strut lined travis is right at home as he installs the led light fixtures and runs his emt conduit between them notice he uses a laser level which ensures the lights are nice and straight as you look down them from one end of the container the customer wants one switch to turn on the lights in both containers so travis will leave a wire loop out of the last light fixture that will have to be connected into the junction box by the electricians at site after this is delivered to the customer this double wide kit will come with these high capacity bridge fittings the one side of them is magnetic and so it'll actually kind of stick and hold into that can the twist locks to slide into the casting first so we'll get these in the four corner castings of the one container and then slide the other one up to it uh when using these it's great when both containers can be sharing the same foundation whether it be a concrete pad or here we got the steel i-beam here so that they stay on the same plane and line up nicely and then there's two different sizes of these this is the bottom corner casting the oval shape there's also one that fits in the shield shape of corner castings and that's for the top because these are typically used when you're putting two 10 foots together to make a 20 foot which can fit now in a vessel slot or you can actually put two 20s together which would make a 40 and it handles just like a 40 with our top lifts so uh they're super strong i think the handle they're rated like 65 000 pounds they're awesome and yeah totally helps us make this double wide kit and then make it possible so it leaves us three inches between the cans which is very nice and useful when it comes to making framing kits and flashing kits and folding special profiles it's a little easier from the top because you can actually get your hand up and inside the corner casting through the top hole and just remember the magnetic side with these is the uh the regular thread and then the non-magnetic side is a reverse thread so that uh once the two cans come together when you use your pry bar or whatever to spin this and suck it all tight the bolt is gonna suck both not in this casting and that casting a big thing with this header kit is you want to make sure that the lower one is here in place first and then you got the the uh higher one with the higher interior flange that comes in afterwards so that you're not uh fighting the design of the header and the way that the the two flashings come together so we have the two halves lined up together and now we're just going to grab our top lift and just nudge it forward we only got to move it about an inch or two forward on these i-beams so slide them together see how these bridge fittings come together and then do the final hook up this is just being test fitted here so we can try out all the flashings maybe pre-drill as many holes as we can for the customer and have it as simple as possible for them to put together when it gets to site so we've slid the two halves together they're not completely together yet but we have the heavy duty bridge fittings in between them now we just need to um tighten them up and that's going to suck the two halves together it's a left hand thread here right hand thread on the other side once we start sucking these together that's going to align the two containers perfectly so you don't have to worry about you know a millimeter here a millimeter there prior to welding these bolts are going to do the work for you once you're all said and done there's this that's just a safety lock so if you put that down then it doesn't allow this bolt to loosen itself off so that was pretty simple inside of a few minutes we have these two 40s put together they're ready to go i really stand by these high capacity bridge fittings i think they're the game changer for us trying to build double-wide kits so now to finish off this enclosure we've got four ridge caps that go on the roof and those get either self-tapping screwed or bolted through the angled profile of this header and then there's two end plates so we've already laser cut and powder coated uh caps that just cover the end here and then this is fully sealed off on this side and then inside the can there's just two channels that close off that three-inch gap so here's the finished product this is what it feels like to be inside two 40-foot shipping containers so way bigger way larger much more usable space once it gets to site the customer is going to be able to remove these temporary transport posts so they'll have that full open clear span they'll weld in their eighth inch six inch wide flat bar along the floor that'll be the threshold plate between the two cans and take up that gap and then we've already test fit the end caps for the end walls here and so that closes everything up there up top they'll bolt the two headers together and then reconnect the wiring on site and this thing's in operation this is such a cool product such a cool mod both times that i've built these for this customer i've wanted to keep them can't wait to get this kit refined even further and get available to you the public and as always if you enjoyed this video please give it a like subscribe to our channel and ring that notification bell check us out at tcg.ca hope you learned something [Music] you
As an Amazon Associate I earn from qualifying purchases.